刘征建1,李思达1,张建良1,3,王耀祖2,王桂林1,牛乐乐1
(1. 北京科技大学冶金与生态工程学院, 北京 100083;2. 北京科技大学人工智能研究院, 北京 100083;3. 昆士兰大学化学工程学院, 圣卢西亚 QLD 4072)
摘要:为了响应国家碳达峰碳中和号召,钢铁企业对于生产节能减排的要求也越来越高,烧结工艺由于在生产过程中固废排放量巨大,因此常常面临限产而导致的烧结产能不足等问题。国内外生产实践表明,高炉高比例球团冶炼具有燃料比低、渣量少等优点,且球团矿性能优良、生产过程更为环保,具有很好的应用前景。为了配合高球比炉料结构的应用,同时避免由于环保限产引起的烧结矿产能不足等问题,国内诸多钢铁企业针对超高碱度烧结矿开展研究。首先从烧结过程和矿物组成变化两个方面对超高碱度烧结矿成矿机理与质量之间的关系进行研究,发现烧结矿碱度在2.10~2.80范围内,随着碱度的升高,矿物主要黏结相逐渐向铁酸钙系黏结相转变,矿物组成逐渐平稳,而碱度大于2.80后黏结相中玻璃质和裂纹逐渐增加,严重影响烧结矿质量。随后对国内典型钢铁企业超高碱度烧结矿生产概况进行了调研分析,并结合矿物学基本原理明确了超高碱度烧结矿与其经济技术指标间的耦合关系。最终提炼出钢铁企业在生产超高碱度烧结矿中出现的问题,基于烧结工艺、矿物学原理及实践经验,探讨了问题的产生原因并提出了相应的解决建议。
关键词: 超高碱度烧结矿;生产实践;冶金性能;技术经济指标;成矿机理
烧结工艺作为中国主要的铁矿粉造块工艺之一,对中国钢铁生产有着重要作用,生产高质量烧结矿是高炉冶炼优质高产的基础。目前中国高炉炉料大多以高碱度烧结矿为主,所占比例为76%左右,同时配加24%左右的酸性球团矿和天然块矿。国内外专家学者对烧结矿原料配比、质量优化、矿相结构等方面进行了大量研究,研究表明,碱度对烧结矿的矿物组成、经济技术指标和冶金性能有着显著影响。20世纪60年代以来,中国烧结矿平均碱度整体呈升高趋势,分为3个阶段:解放初期,中国刚刚步入炼铁行业,铁产量低、质量差、焦比高,钢铁企业主要使用自然碱度烧结矿并配有天然块矿进行高炉冶炼;1960-1970年,随着炼铁工艺技术的不断进步,中国钢铁企业开始使用自熔性烧结矿单一炉料进行冶炼生产,冶炼技术相比解放初期有了较大提高;1970年以后,中国开始推广使用高碱度烧结矿进行炼铁生产,加之天然优质块矿储量逐渐降低,高碱度烧结技术迅速发展,中国高炉入炉炉料逐步发展为如今的以高碱度烧结矿为主,配加酸性球团矿或酸性块矿的炉料结构。在实际生产中,中国大部分钢铁企业生产的高碱度烧结矿的碱度范围在1.80~2.10之间,所以对于部分钢铁企业所生产的碱度大于2.10的烧结矿,一般认为是超高碱度烧结矿。为了响应国家碳达峰碳中和号召,钢铁企业对生产节能减排的要求也越来越高,烧结工艺由于在生产过程中固废排放量巨大,因此常常面临限产而导致的烧结产能不足等问题。而相比于烧结,球团制备过程在节能环保、粒度、性能等方面有着巨大优势,同时对高炉技术经济指标也有着重要意义。因此,提高球团矿的配比逐渐成为中国高炉炼铁行业研究热点。高球团比冶炼条件下,生产并采用超高碱度烧结矿成为平衡高炉炉料碱度的重要途径。基于此,本文旨在对超高碱度烧结矿技术进行调研总结,为钢铁企业超高碱度烧结矿的生产实践提供经验。本文主要对国内典型钢铁企业超高碱度烧结矿生产概况进行调研分析,并且结合矿物学基本原理明确了烧结矿超高碱度与其技术经济指标的耦合关系,探讨了超高碱度烧结矿生产过程中易产生的问题并给出了相应的解决建议。1.1超高碱度烧结矿对烧结过程影响分析
超高碱度烧结工艺即在混合料中配加大量熔剂,得到碱度大于2.10的超高碱度烧结矿。在超高碱度烧结生产过程中,大量熔剂的加入会使得烧结料层透气性得到明显改善,在烧结速度加快的同时,高温持续时间缩短;熔剂所占比例提高也会使得烧结矿在烧结过程中更容易形成低熔点物质(Fe2O3·CaO)同时抑制FeO的生成,从而使得烧结混合料熔化温度降低,液相量增加,进而提高了烧结混合料的黏结能力。但是提高烧结矿的碱度也会随之带来一系列问题,例如,熔剂的增加会降低成品矿铁品位,同时也极易产生大量的游离CaO,在成品烧结矿中出现“白点”现象,这些分散于烧结矿内部的游离CaO遇水消化易发生膨胀并最终影响烧结矿的强度。烧结过程中液相量的增加、烧结速度的加快、高温持续时间缩短均不利于烧结脱硫,同时高温下石灰对硫的吸附作用增强,从而降低烧结过程脱硫率。1.2超高碱度烧结矿成矿机理分析
从烧结矿成矿机理方面来看,提高碱度所带来的最明显改变则是烧结矿黏结相的变化,碱度在2.00~2.80范围内,即超高碱度条件下,烧结矿主要黏结相为铁酸钙系黏结相:在碱度为2.00时,黏结相主要为铁酸钙,且多为板状结构、部分为针状交织结构,同时含有少量的钙铁橄榄石和钙镁橄榄石;碱度约为2.40时,主要黏结相变为铁酸钙,铁酸钙体系(CaO·Fe2O3-Fe3O4)和钙镁橄榄石,钙铁橄榄石消失,黏结相多为针状交织结构,部分为板状结构,整体结构趋于均匀;碱度为2.80时,烧结矿主要黏结相变为铁酸钙、铁酸二钙和钙镁橄榄石,黏结相中出现玻璃质并且裂纹增多,使得烧结矿强度明显降低。从成矿机理角度分析可知,碱度2.40为超高碱度烧结矿的矿相特征分界点,而碱度2.80则为超高碱度烧结矿的质量分界点,碱度高于2.80时,烧结矿质量将会呈严重下滑趋势。当烧结矿碱度不超过2.40时,随着碱度增加,烧结矿黏结相形态变为强度更高的针状交织结构,有利于提高烧结矿的转鼓强度;碱度增加也使得铁酸钙生成能力增强,抑制了铁橄榄石的形成,提高了烧结矿的低温粉化还原性能,同时也使得烧结矿还原性能得到改善。碱度超过2.40以后,烧结矿黏结相整体结构趋于均匀,冶金性能增幅逐渐变缓,而随着碱度进一步增加,矿相中出现玻璃质及内裂纹,使得烧结矿强度大幅降低,同时较难还原的铁酸二钙含量增加,也降低了烧结矿的还原性。此外,烧结矿中SiO2、MgO及Al2O3等化学组分对超高碱度烧结矿矿相结构及含量也有着一定影响。相同碱度条件下,高SiO2含量可提高烧结液相量,有利于改善烧结矿强度,但会降低成品矿含铁品位,增加吨铁渣量,提高产品成本;原料中Al2O3的存在形式及反应性会影响复合铁酸钙的生成量及结构,适量的Al2O3能够有效促进复合铁酸钙的生成,而铝元素含量过高、硅铝比过低则会导致铝元素向玻璃相富集,引起烧结矿强度降低;烧结原料中过量的MgO含量会抑制磁铁矿的氧化,降低烧结矿复合铁酸钙的含量。综上所述,烧结矿碱度与其他化学成分等对烧结矿质量的影响存在复杂的耦合关系,所以在超高碱度烧结矿的成矿过程中需要进一步控制不同组分间的影响。通过查阅文献及现场调研,总结了目前国内钢铁企业实行超高碱度烧结生产相关数据、设备参数及经济技术指标。由前文超高碱度烧结矿成矿机理分析研究可知,碱度2.40为烧结矿物相及性能演变的转折点。当烧结矿碱度低于2.40时,提高碱度会使铁酸钙系黏结相所占比例提高,有利于改善烧结矿转鼓指数及冶金性能;而当碱度高于2.40时,铁酸钙系黏结相生成量随着碱度升高逐渐趋于平稳,对其冶金性能影响幅度逐渐减小。据此,将超高碱度烧结矿生产实践分为低于2.40碱度和高于2.40碱度两类进行分类总结,具体情况如下。2.1碱度低于2.40超高碱度烧结矿生产实践
近年来,随着宣钢高炉原料需求量持续增长,其烧结矿产量供给出现供不应求的状况。为了解决高炉原料需求问题,宣钢决定逐步提高烧结矿碱度,并配以大比例球团来保证高炉原料充足,经过4个月时间,宣钢烧结矿碱度由2.00升至2.24。同时迁钢也实施超高碱度烧结矿生产,提高烧结矿碱度以提高酸性球团矿入炉比例、降低烧结矿的使用,迁钢所生产的烧结矿碱度已提高至2.29左右。通过对原料和烧结设备参数两个方面进行改进,有效地实现了超高碱度烧结矿的优质、稳产。2.1.1烧结原料成分和粒度控制
针对碱度低于2.40的超高碱度烧结矿生产,需要合理控制烧结原料的成分和粒度。由于在超高碱度条件下,SiO2含量的轻微波动就会导致烧结矿碱度发生巨大变化,所以在配料过程中,需要严格控制SiO2含量、加强原料混匀、稳定熔剂质量以保证在生产超高碱度烧结矿过程中成品矿碱度的稳定性。粗粒级熔剂在混匀制粒过程中易成为核颗粒,这些被矿粉包裹的熔剂是烧结矿出现“白点”现象的主要影响因素,而超高碱度烧结生产中需要配加大量熔剂,所以超高碱度烧结生产对于熔剂粒级分布的要求更为严格。据调研,宣钢烧结用生石灰粒度不大于3 mm部分严格控制在85%以上,CaO质量分数控制在74%以上。2.1.2超高碱度烧结工艺参数调整
生产实践表明,大量熔剂的加入使得超高碱度烧结过程料层透气性增加,烧结速度加快,所以需要延长高温保持时间以促进矿物结晶。宣钢烧结工艺改进前后的重点工艺参数对比见表1,为了匹配超高碱度烧结矿生产工艺,宣钢选择提高料层厚度和降低负压的方式来延长烧结高温保持时间,其中料层厚度由730提高至750 mm,烧结负压由15.6降低至14.7 kPa,并在烧结之前对混合料进行压料处理;由于生石灰用量提高,所以加水量随之上升,控制水分在7.3%左右。迁钢超高碱度烧结生产料层厚度控制在750~790 mm,烧结机机速最低可达1.8 m/min,垂直烧结速度控制在19.5 mm/min左右以保证烧结燃料充分燃烧,烧结负压控制在13 kPa左右来保证烧结过程适宜的透气性。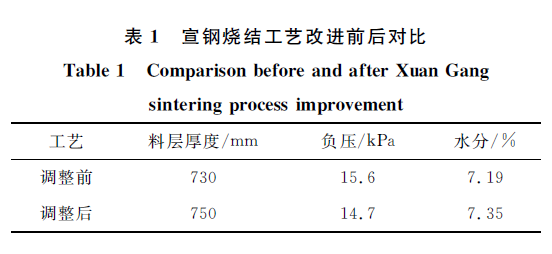
2.1.3超高碱度烧结技术经济指标
4个月以来,宣钢逐步提高生产碱度后对各项烧结指标的影响见表2,由表2可知,随着碱度的提高,料层中熔剂含量逐渐增加,铁矿粉所占比例相应降低,进而呈现出烧结矿铁品位降低趋势;石灰石分解为吸热反应,其配比的增加使得固体燃耗相应提高;料层透气性的改变提高了垂直烧结速度,进而影响了烧结利用系数及成品率。调研数据表明,平均碱度每升高0.1,其固体燃耗增加0.55 kg/t、成品率降低0.71%、铁品位降低0.25%。迁钢超高碱度烧结矿的化学组成和部分烧结指标分别见表3和表4,可以看出,迁钢对原料化学成分和粒度的控制,成品铁矿品位稳定率、碱度稳定率和一级品率均严格控制在100%,转鼓指数达到84.2%,烧结矿质量进一步改善。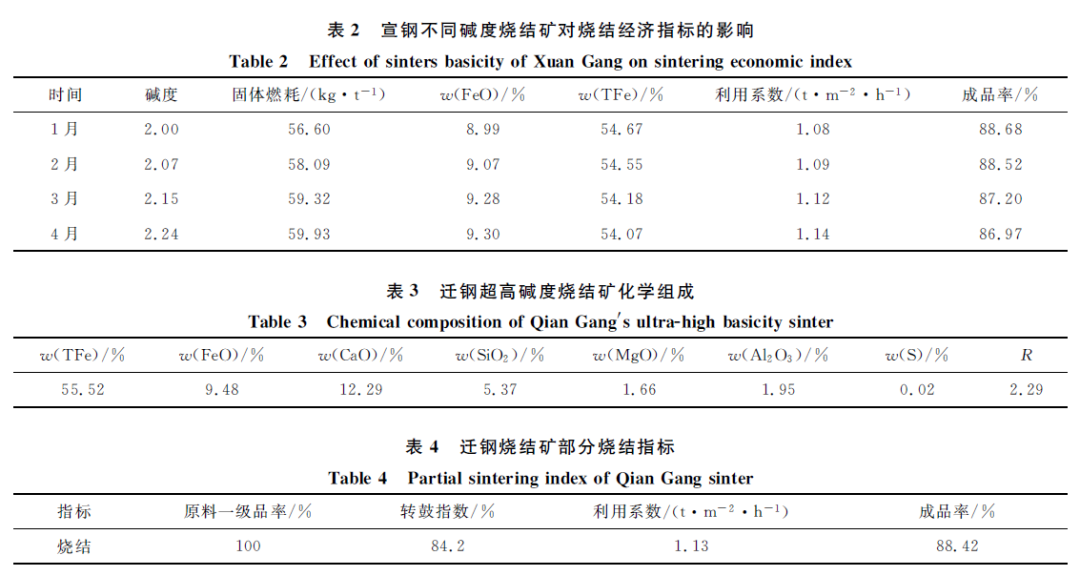
2.2碱度高于2.40超高碱度烧结矿生产实践
当碱度高于2.40后,为了保证烧结矿铁品位及经济效益,钢铁企业往往通过降低SiO2含量(硅质量分数降至5%以内)来提高烧结矿碱度,而烧结矿SiO2含量的降低会造成烧结液相量减少,且脉石含量不均匀引起的碱度波动使得黏结相中铁酸二钙和玻璃相含量的增加,最终导致烧结矿强度降低及冶金性能劣化。因此高碱度烧结矿对原料化学成分及粒度的控制提出更高的要求,需要根据原料自身特性进一步优化配比以满足超高碱度烧结矿生产。2.2.1烧结技术经济指标及冶金性能
凌钢烧结矿碱度高达2.45,经过优化配矿后,对不同种类铁矿粉烧结原料进行合理搭配,降低了烧结成本,满足了碱度高于2.40的烧结矿生产,使得成品矿质量整体改善。在超高碱度条件下,凌钢烧结矿转鼓指数为76.81%,固体燃耗为56.30%,利用系数为1.51 t/(m2·h)。可以看到,凌钢超高碱度烧结利用系数相对于其他企业较高,固体燃耗相对较低,原因是优化配矿过程做到了铁矿粉基础性能合理搭配、优势互补。后续对凌钢现场烧结矿取样并进行还原性、低温还原粉化性及荷重软化熔滴性能等冶金性能检测,检测结果见表5。凌钢生产超高碱度烧结矿的还原性与低温还原粉化性能(RDI>3.15 mm)相对较低。烧结矿成矿机理表明,碱度提高有利于针状铁酸钙系黏结相的生成,故而对烧结矿强度及冶金性能均有促进作用,但钢铁企业为保证烧结矿铁品位,一般通过进一步降低硅含量而实现超高碱度烧结矿的生产。因此硅含量的降低影响了烧结过程中黏结相含量,进而使得烧结矿强度及冶金性能降低。此外,熔滴性能检测结果表明,凌钢所生产的烧结矿软化区间较窄但熔融区间较宽,不利于高炉滴落带透气性。影响烧结矿荷重软化性能主要有两个因素:烧结矿还原性能的改变使得烧结矿液相生成温度提高,进而导致高炉中烧结矿的软化开始温度升高;碱度的提高也会使得烧结矿熔点升高,从而提高烧结矿软化开始温度。所以在超高碱度范围内,提高烧结矿碱度可以使得软化开始温度升高,缩小软化区间,有利于高炉透气性的改善。但碱度过高也会使得熔融开始温度降低,熔融区间变宽明显,透气性的减少使得熔融终了温度大幅增加,对高炉顺行不利。
2.2.2超高碱度对钒钛磁铁矿烧结的影响
攀枝花钢铁公司炼铁厂烧结所使用的主要含铁原料为钒钛磁铁矿精矿粉。2006年以来,攀钢将高铁低硅烧结生产作为攀钢烧结技术发展的方向,其碱度为2.45左右,并于2018年通过优化配矿以及改进烧结机参数等方式,实现了碱度为3.30的超高碱度烧结矿生产工艺。由于钒、钛等元素的存在,使得碱度对钒钛烧结矿矿相特征及冶金性能的影响幅度及影响趋势明显不同于普通烧结矿。蒋大军等基于攀钢现场钒钛烧结矿原料配比进行的不同碱度烧结杯试验结果见表6。由表6可知,随着烧结矿碱度的提高,熔剂配比逐渐增加,铁矿粉所占比例相应降低,使得烧结矿全铁质量分数由49.4%逐渐降低至47.1%;熔剂所占比例的提高也使得烧结料层透气性增加,进一步提高了垂直烧结速度及利用系数,但高温保持时间缩短,降低了烧结矿成品率;由于石灰石分解属于吸热反应,所以随着石灰石配比的增加,烧结过程中热量消耗也进一步增加,固体燃耗由56.63逐步提高至62.21 kg/t。文献研究表明,钛含量过多对烧结矿强度有不利影响,而提高烧结矿碱度抑制了钛铁矿对攀钢烧结矿强度的不利影响, 改善了烧结矿强度。不同碱度的钒钛烧结矿还原性能和低温还原粉化性能对比结果见表7,烧结矿碱度由2.00提高到2.95,其还原性和低温还原粉化性均得到改善。但碱度达到2.60后烧结矿还原度RI增幅变缓,碱度达到2.80以后烧结矿低温还原粉化指数降幅变缓,这是由于碱度提高使得钛磁铁矿、钛赤铁矿的含量降低,强度及还原性均较好的铁酸钙相增加,从而使得烧结矿还原性和低温粉化还原性明显改善。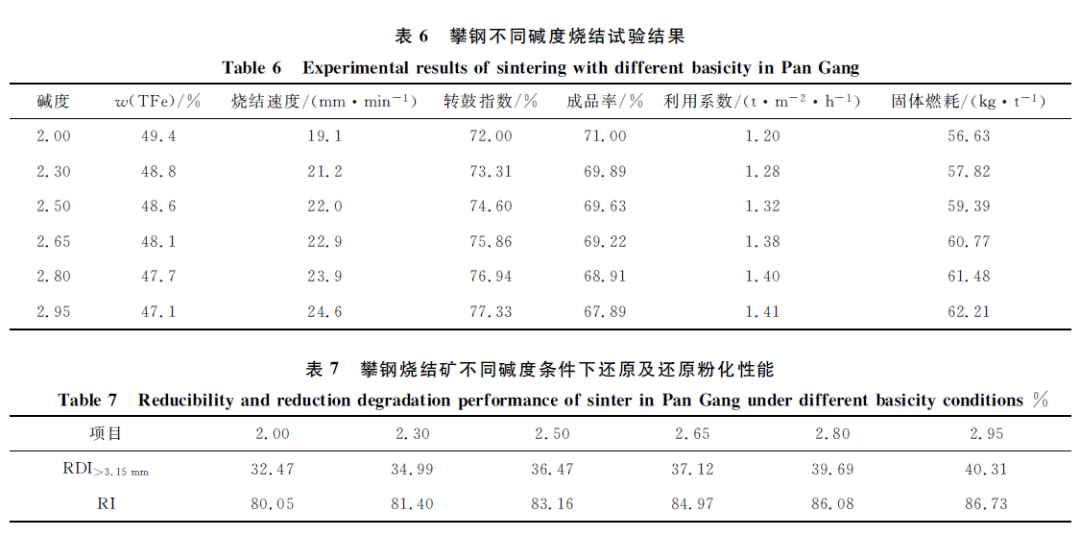
超高碱度对攀钢钒钛烧结矿荷重软化性能影响如图1所示。由图1可知,碱度的提高使得钒钛烧结矿软化温度由1 117提高至1 155 ℃,这与非钒钛烧结矿熔滴性能变化趋势相一致,碱度的提高可使钒钛烧结矿软熔带变窄,高炉软熔带逐渐下移,进而改善料柱透气性。通过图2熔融终了温度变化规律发现,碱度的提高对钒钛烧结矿中矿物熔点影响较小,熔融终了温度基本维持于1 515 ℃左右。因此碱度的提高可以改善钒钛烧结矿熔滴性能。通过对超高碱度烧结矿的研究,蒋大军等确定了攀钢烧结矿最适宜的碱度为2.80,其烧结指标及冶金性能都非常良好。攀钢在烧结工艺参数上通过降低机速、降低负压、厚料层烧结等措施以优化超高碱度烧结矿的生产:超高碱度烧结负压比烧结普通碱度烧结矿的负压低3~5 kPa,优选负压为10~12 kPa;超高碱度烧结混合料粒度不小于3 mm占70%~80%并且强化活性石灰的使用;料层厚度为700~750 mm。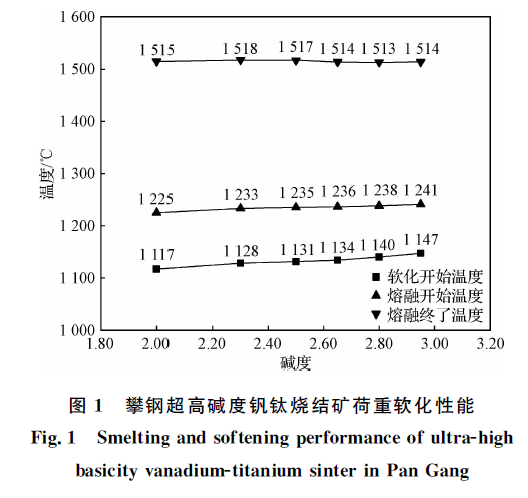
近年来,烧结工作者们针对超高碱度烧结矿生产实践中出现的诸多问题提出许多解决措施。综合生产实践及矿物学原理分析,汇总整合了以下改善方案。(1)相比于高碱度烧结矿,超高碱度有助于提高烧结过程料层透气性,使得燃料燃烧速度加快,保温时间变短。钢铁企业一般通过改变机速、负压等方式来减缓垂烧速度、提高保温时间。此外,也可结合气体料面喷吹技术,增加烧结过程中燃烧带宽度,延长烧结保温时间,使烧结过程液相结晶更加充分,同时也有助于减少烧结固体燃料消耗,降低烧结成本,提高烧结效益。(2)烧结过程熔剂活性、制粒过程消化工艺及高温过程与矿石矿化程度均会影响熔剂的反应行为,超高碱度烧结生产需要配加大量熔剂,亦容易在烧结矿中出现“白点”现象。生产实践表明,需要在严格控制熔剂粒度的同时,结合生石灰预消化处理技术,或是使用高活性石灰以减少“白点”现象的出现。此外,熔剂的增加也使得烧结矿中硫含量增加,但当烧结矿碱度高达4.0时,其内部大多生成了稳定的CaSO4,有待进一步研究明确对后续工艺的影响。(3)有效控制烧结矿碱度波动是实现超高碱度烧结矿稳产的一大技术难点,需要对烧结原料进行优化配比才能有效改善。针对烧结用不同矿粉种类,合理搭配原料结构,严格控制烧结原燃料粒度分布,合理调整硅铝比、MgO含量以及ZnO含量等化学成分,有助于改善烧结矿碱度和成分波动问题。此外,在传统烧结混合制粒流程中增添强力混合工艺,以避免制粒过程所引起的化学成分偏析现象。随着含铁原料品种逐步增加且成分波动变化,烧结过程动态时变且复杂滞后,传统周期性采样对烧结矿进行化学检测的方法并不能满足烧结矿碱度稳定控制的需求,在如今人工智能等新兴技术逐渐工业化应用的时代背景下,发展烧结工序在线成分质量预测系统对于烧结矿碱度波动控制具有重要意义。实时检测烧结混合料及成品矿化学成分变化,减少矿种成分波动所带来的化学成分差异,进一步改善和控制烧结矿碱度及化学成分的稳定性,以实现烧结矿品质的智能化管理。
(1)通过在烧结过程中配加大量熔剂,提高二元碱度至2.10以上,从而得到超高碱度烧结矿。通过对超高碱度烧结矿成矿机理进行分析得出,碱度在2.10~2.40之间时,随着碱度升高,铁酸钙黏结相含量逐渐增高且由板状结构向针状结构发展;碱度在2.40~2.80之间时,矿相变化逐渐趋于平稳,主要黏结相为铁酸钙,铁酸钙体系(CaO·Fe2O3-Fe3O4)和钙镁橄榄石;而当碱度高于2.80时,黏结相中铁酸二钙含量逐渐增多并伴随玻璃质和裂纹的出现。碱度2.40为超高碱度烧结矿的矿相特征分界点,在烧结矿碱度低于2.40时,提高其碱度可使得烧结矿还原性、低温还原粉化性能、荷重软化性能均有较大改善,碱度高于2.40后,增幅效果逐渐缓慢。碱度2.80为超高碱度烧结矿的质量分界点,碱度高于2.80时,烧结矿质量将会呈严重下滑趋势。(2)在生产超高碱度烧结矿过程中,钢铁企业通过对原料成分和粒度的合理把控、对烧结设备的设计改进以及对烧结过程的严格控制,可有效解决超高碱度生产所带来的烧损严重、成品率下降等问题。而由于钢铁企业往往利用低硅烧结工艺来进一步提高烧结矿碱度,此时则对其化学成分的稳定控制提出了更高的要求,在对烧结设备参数改进的前提下,还需要通过优化配矿、强力混合、预消化石灰等措施来进一步加强对烧结原料成分的控制,以实现其稳定生产。(3)由于钒、钛等元素的存在,使得碱度对钒钛烧结矿的矿相特征及冶金性能的影响幅度及影响趋势明显不同于普通烧结矿。通过攀钢不同碱度烧结杯试验结果分析得出,提高碱度可以有效规避钛含量过多对烧结矿强度的影响,同时也使得强度及还原性均较好的铁酸钙系黏结相含量增加,有效改善了钒钛烧结矿的冶金性能。此外碱度的提高也可以使得钒钛烧结矿软熔带变窄,促进高炉软熔带下移,从而有助于改善料柱透气性。(4)针对钢铁企业在生产超高碱度烧结矿中出现的问题,基于烧结工艺、矿物学原理及前人实践经验,对其中存在的问题提供了解决建议及未来展望。虽然在实际生产中超高碱度烧结矿仍然存在许多问题尚未彻底解决,相信在可预见的未来,随着烧结工作者们坚持科学指导,理论结合实践,对这些问题进行深入研究并逐个击破,超高碱度烧结矿生产必将会成为在高比例球团冶炼的大形势下典型铁前原料生产方式之一。